Lean Tool Series
Empowering people with knowledge to elevate companies to excellence.
Like all good Lean journeys, this is a work in progress. In true Agile fashion, we'll be posting new tools, resources, ideas, information, and training opportunities as we develop them. Bookmark this page, and check back from time. Have something, in particular, you'd like to see? Contact us anytime. Thanks for joining us!
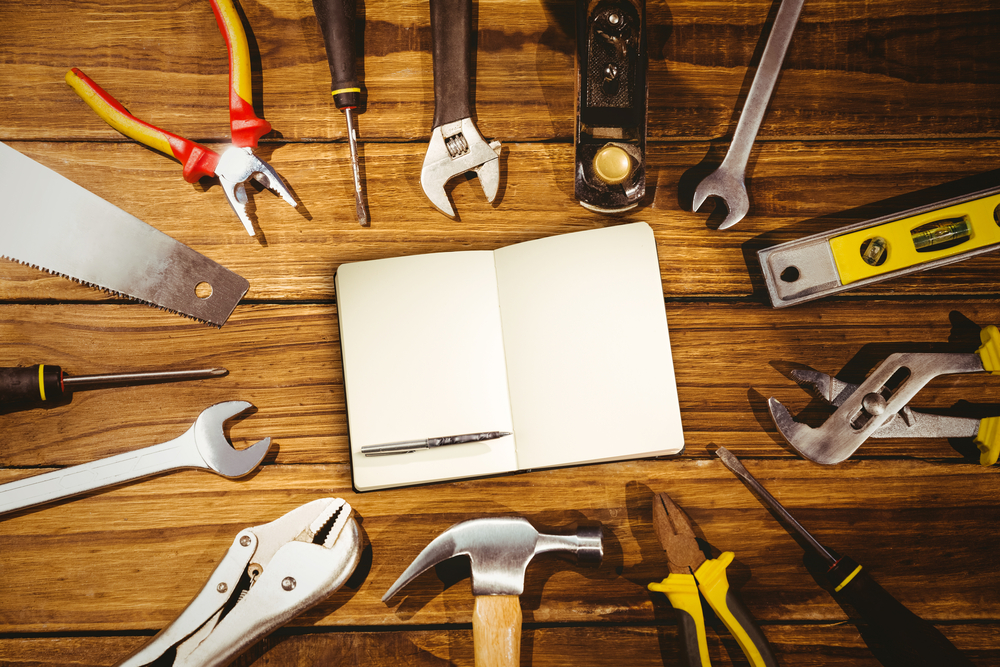
Welcome to the Lean Tool Series
Flaws in processes, not in people, are at the root of almost all inefficiencies and issues in business. With an understanding of basic Lean principles and a selection of tools to identify, analyze, and address process issues, your organization can EMPOWER EXCELLENCE in your people and move toward more efficient, customer-focused, profitable, Lean operations.
Whether you’re a newcomer to Lean or a seasoned practitioner, a quick primer (or reminder) about Lean Principles and Lean Tools is a good place to start our journey.
With How-To-Guides, checklists, actionable templates, and other resources, the Lean Tool Series will help you learn, teach, implement, and optimize the use of Lean Tools in your organization.
We're here to support your Lean Journey, no matter what your job title, industry, or level of experience.
WorkPlace Organization
(or 5S)
A simple but highly effective set of techniques, 5S works to remove waste from an environment through better workplace organization, visual communication, and general cleanliness.
The primary benefit of 5S is improved efficiency by eliminating waste related to looking for, moving, or storing things or information. Implementing 5S can also improve safety and quality by removing excess steps and standardizing optimal patterns and can increase worker satisfaction by creating a better work environment.
"A Place for everything and everything in its place."
Based on Japanese principles, 5S is 5 steps to implement order in a workplace:
SORT (Seiri): The first step in the 5S process, SORT involves clearing the workspace of all materials that are not necessary to the work process. A basic formula is to keep things that are needed for the functioning of the workspace, return any items that belong in other workspaces or departments, and get rid of everything else. While sorting will look different in various workplaces, the goal is to eliminate obstacles and distractions (wastes) from the area to make accomplishing the work easier.
STRAIGHTEN (Seiton): After unnecessary items and distractions have been cleared, next, STRAIGHTEN (or, set in order, simplify). Put all necessary items (those not eliminated in the SORT step) in close proximity and arrange them by their uses with the most often used items the closest. This improves the workflow by eliminating wasted time looking for and/or moving to/from needed items. Label everything.
SHINE (Seiso): With the workplace set in order, the next step is to clean daily or on a regular schedule that works for the space. The SHINE (or scrub) step creates a more positive atmosphere for employees which supports productivity as well as provides for regular inspections that can prevent the deterioration of equipment and tools. A clean, organized workspace is also a safer workspace.
STANDARDIZE (Seiketsu): The fourth step in the 5S process, STANDARDIZE is establishing the structure (procedures, schedules, audit checklists, etc.) that ensures consistent implementation of the first 3 S's - sorting, organizing, and cleaning. This step ensures that everyone knows their individual responsibilities and supports making the practices part of the daily routine. Photos, visual controls, color coding, and other organizing tools should be used to keep everything in order.
SUSTAIN (Shitsuke): The final 5s step is SUSTAIN (or systematize), which also translates as, "do without being told". This is the step that turns a one-time "clean-up" into a way of doing business. Goal-oriented training sets the foundation—learning the process and developing the discipline to follow the established process while also being open to improvement. Sustaining (maintaining proper order) should include training, discipline, and regular audits as well as consistent feedback. This is the most difficult step because it requires developing new habits and expectations and then supporting those involved as the new habits become the new standard way of working.
- SAFETY. Sometimes called out as the 6th S, safety means eliminating hazards in the workplace. Clearly mark or make adjustments to areas that have a potential for injury. Whether included as part of the 5S above or added separately, ensuring a safe work environment is fundamental to respecting employees and operating successfully.
As practical and straightforward as 5S is, it, of course, looks different in various industries, organizations, and facilities and sometimes even in different departments within the same organization. What is important is to be clear on both why and how it is being done.
The initial process and the plan for sustaining must be clear to all involved and supported and reinforced by management. A cleaner, more organized workspace pays dividends through improvements in safety, productivity, and employee satisfaction and is a solid foundation to build further continuous improvement efforts.
Want to read more about Workplace Organization? We recommend Hiroyuki Hirano’s 5S for Operators: 5 Pillars of the Visual Workplace.
Free Download
A Complete Pillar Strategy Guide
Everything you need to start creating your pillar page flows today.
Call to ActionValue Stream Mapping (VSM)
Value Stream Mapping is a macro-level view
Value Stream Mapping is the visual representation of all of the value-added and non-value-added activities that occur to complete an operation or process.
Value Stream Maps show the flow of a process from the perspective of the customer. By visualizing the flow of a process at a macro level, teams can see how the entire process works, understand actual performance, and identify areas to create added value and eliminate waste.
5 Steps of Value Stream Mapping
In creating a VSM, the entire process flow of information and materials needed to create a product or service is documented visually as it is currently being performed. This is known as the "Current State Map," which makes it possible to identify each step in the process as:
- Value-added, activities that add real value or worth to the product or service—usually something the customer is willing to pay for;
- Non-value-added, activities that do not add real value or quality to a product or service—something the customer will not pay for and should be considered for elimination; or
- Non-value-added but necessary, activities that are important to the company and/or necessary to do the job, but that the customer will not pay for; these should be minimized/controlled as much as possible without compromising the end product.
Once the Current State Map is drawn and wastes identified, the information revealed is used to determine ways to reduce or eliminate waste (non-value-added items) and optimize value-added items.
Standard Work
Standard Work is the foundation on which processes are built and improvements are made.
Standard Work, or Standardized Work/Standardized Operations, is specific, documented best practices for tasks, processes, procedures, and activities to reduce variation, one of the forms of waste in Lean. Standards must be measurable and repeatable to be consistently and efficiently implemented.
Standard Work is essential to effective work at all levels and in all areas of an organization, including quality and process specifications, policies and procedures, regulatory compliance, and technical standards. Every routine task should be standardized, beginning with those that directly impact the company's ability to meet customer demands.
Standard Work provides the basis on which the actual performance of a process is judged and, therefore, establishes the foundation for future improvement. It creates a clear picture of a properly operating process so variations from that can be identified and addressed systematically rather than trying random tweaks and "fixes" to make ad hoc improvements. Without standardization, it's impossible to see clearly what needs to be improved and whether or not attempted improvements have any effect.
6 Steps of Standardized Work
- Check facilities, systems, and equipment: Ensure everything needed to successfully implement the process is in optimal working order.
- Check timing: Measure the time it takes to complete a work cycle (productivity rate), compare it to the pace of work needed to meet customer demand (takt time), and make adjustments to improve the productivity rate as needed (not to takt time).
- Check work-in-process inventory: Look for ways to reduce the amount of inventory that needs to be staged rather than pulled through a process as needed. Document a range of acceptable inventory.
- Issue Standard Work Instructions: Establish clear, measurable instructions that will be easily understood and easily followed by those doing the work. Issue instructions in whatever format best suits the process and the people implementing it — signage, instruction sheets, manuals, etc. (Pro tip: When you can, "poke-yoke" your instructions — error-proof them by not only making them easy to follow but preventing them from not being followed.)
- Monitor and Measure: After implementation, observe results and compare them to the established standard. Look for variations and waste, and make corrections to get back to the standard.
- Make Improvements: Evaluate the effectiveness of your standard work over time, work with your team to determine and evaluate potential improvements (Kaizen events), and make updates to the standard work as needed. Ensure all changes are documented as precisely as the original and changes are made and implemented quickly. Like software updates to optimize performance, standard work updates should be a normal and expected part of the routine.
Toyota Kata
From the Japanese, a kata is literally a model or pattern, a set of positions and movements (as in karate), any basic form, routine, or pattern of behavior. Established and recognizable patterns make it easier to see unusual movements or issues and provide a clear foundation for improvement.
“Toyota Kata” is the term that Mike Rother (internationally recognized Lean guru and author of Learning to See) coined to help American manufacturers mirror Toyota’s successful practices of true continuous improvement.
The Kata model is grounded in the philosophy that by teaching workers (or in kata, learners) to think and act scientifically, we can build a culture where every employee is educated and empowered to be a better problem-solver.
Kata Methdology: Improvement Kata and Coaching Kata
Rather than specialized staff members executing one-off, resource-intensive “improvement projects,” practicing the Kata helps every member of an organization become skilled in seeking improvement every day.
The Kata consists of the Improvement Kata (IK) and the Coaching Kata (CK), which form a structured pattern for making small incremental improvements every day.
The Improvement Kata is a model of the human creative process. It’s a four-step pattern of establishing target conditions and then working iteratively (scientifically) through obstacles by learning from them and adapting based on what's being learned.
The Coaching Kata is a pattern for managers to follow in teaching the Improvement Kata pattern in daily work so that it becomes part of an organization's culture.